Example of improvement of floor shaking problem caused by a press machine in a factory
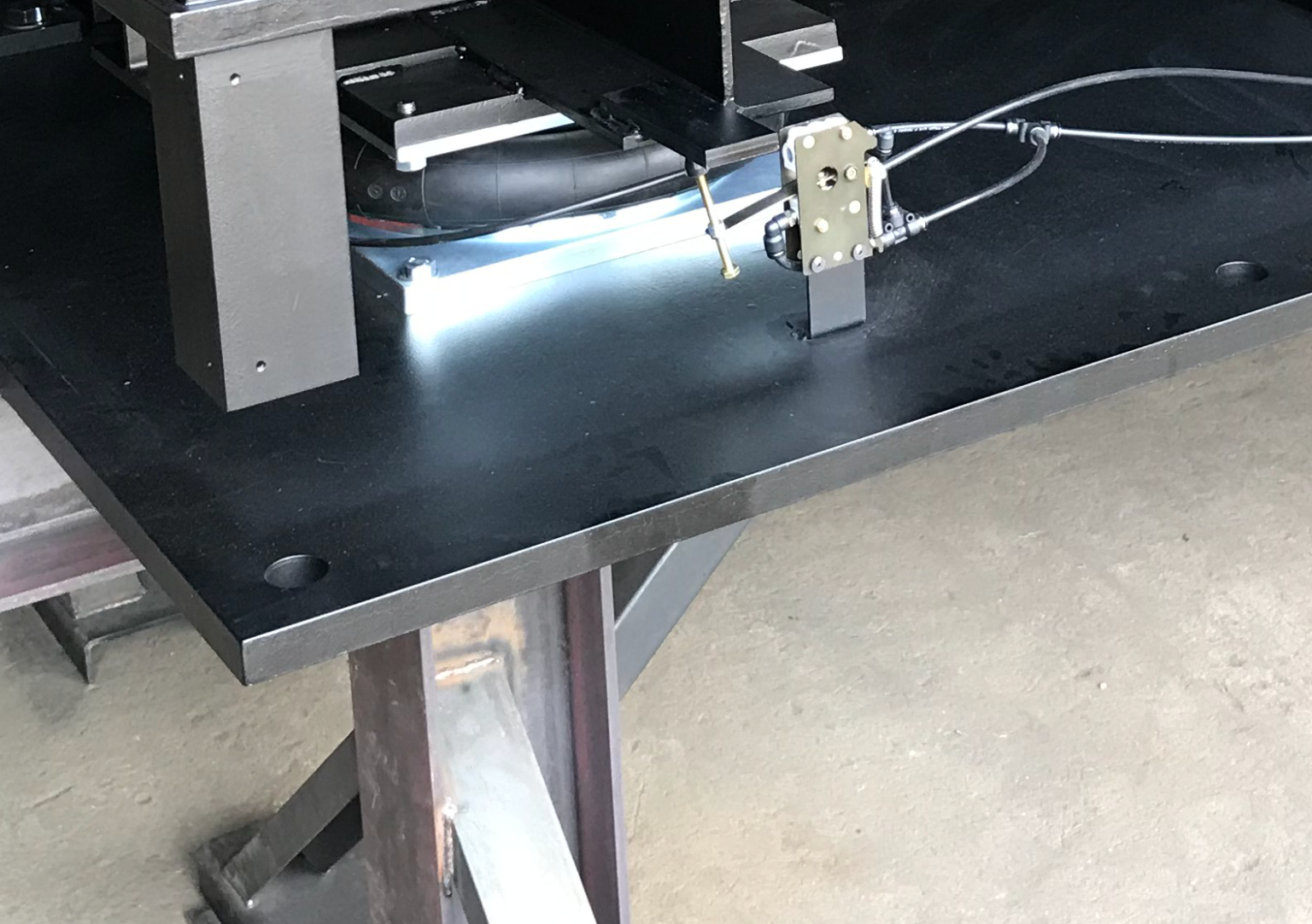
A new production machine was to be introduced at a certain factory. When a new press machine was introduced, there were concerns that the large vibratory force would deteriorate the work environment and affect the neighborhood. By installing anti-vibration equipment, we were able to reduce the vibration transmitted to the surrounding area and improve the work environment and impact on the neighborhood.
issue
Among the machines that operate in production plants, hydraulic presses (hot forming machines) have particularly high excitation forces and often create vibration problems.
When a new 30-ton press was installed at Company N's plant, there were concerns about the vibration generated by the press operation, which could shake the floor of the workshop and affect the neighborhood.
The factory was also located in an industrial area (Class II) with vibration regulations of 65 dB during the day and 60 dB at night.
Therefore, the customer requested that the vibration level be reduced to 60 dB at 1 m from the press.
Furthermore, because the machine is newly installed, it is not possible to measure the vibration in advance to see what kind of shaking is occurring. It was decided to estimate how large the vibration would be when the press was newly installed based on the machine specifications.
The magnitude of vibration of the machine foundation in non-vibration-proof condition is estimated based on the machine data given by the customer.
The result is a maximum velocity of 3 mm/s, which translates to a vibration level of approximately 73-74 dB.
Large vibrations in excess of the requested 60 dB were expected. (Figure 1).
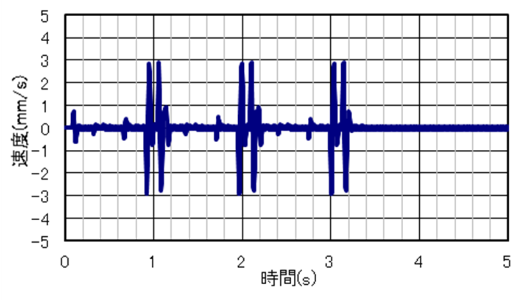
counter-measure
As a countermeasure, a proposal to install an air-spring vibration isolator under the press was suggested.
At this time, it is essential to note that the vibration isolator is an elastic body, so it must not affect the machining accuracy of the machine.
First, a study was conducted to confirm that the machining accuracy of the machine would not be affected when air springs were used to isolate vibration. Based on the operating pattern of the operating section, we assumed the excitation force, and the predicted displacement of the machine was examined, and the results satisfied the product specifications of 3 mm or less in the vertical direction (Figure 2).
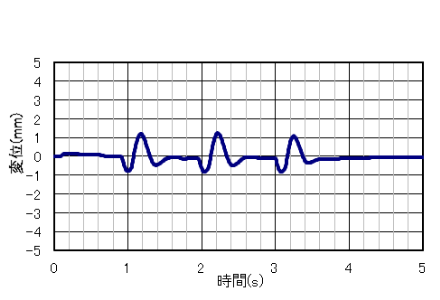
Figure 2: Predicted values of machine displacement
When the vibration isolation effect was predicted and examined in advance, the expected vibration isolation effect was estimated to be 15 dB, taking into account the rigidity of the plant foundation, the type of press, the predicted transmission coefficient based on the vibration isolation theory, and our knowledge.
After discussions with the customer, a policy was decided to use air springs to satisfy the vibration level of 60 dB after countermeasures.
(-15dB vibration isolation before 73-74dB measures = 58-59dB after measures <60dB)
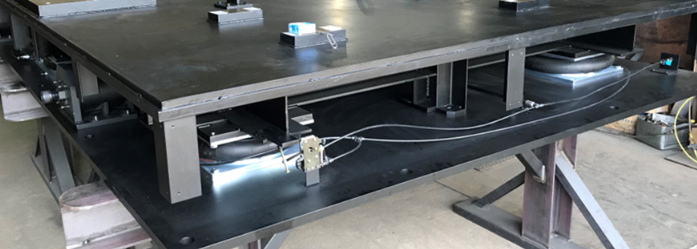
Figure 3: Appearance of air spring vibration isolator
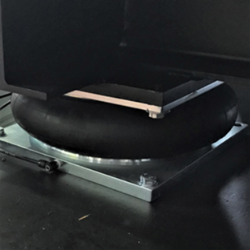
Figure 4: Appearance of air spring
Table 3: Basic Specifications of Vibration Isolators
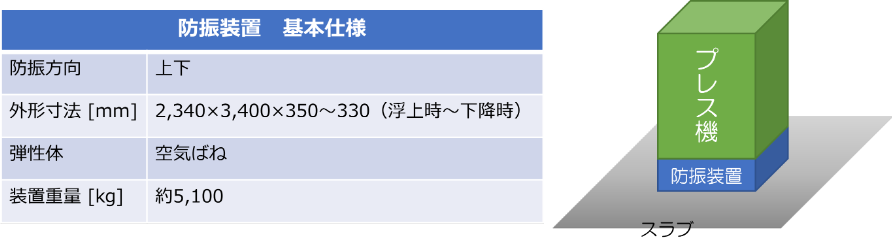
result
Vibration levels were measured after installation of the vibration isolator.
At 1 m from the press, the machine vibration environment was greatly improved to approximately 50 dB. (Figure 5).
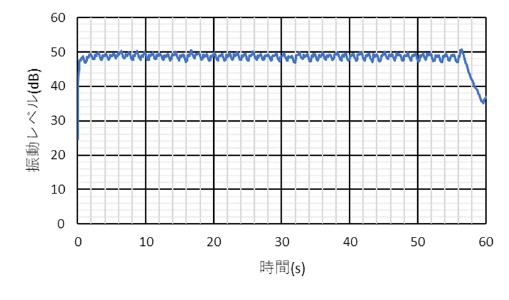
Figure 5: Time history vibration levels after vibration isolation measures [dB].
Related Pages
- Trivia] Basic Knowledge of Vibration Suppression - What is the difference between "anti-vibration," "vibration isolation," and "vibration suppression"? ~Vibration Isolation
- Product Information] Air Springs
Related Content
- Yacmo's Vibration Prevention Map by Usage Scenario
- Technical Column] Countermeasures for Vibration Problems Caused by Production Equipment Machinery and Examples of Improvements
- Technical Column] Types and Features of Measures to Reduce Floor Swaying Caused by Walking and Machinery
- Webinar Video] Countermeasures for Mechanical Vibration Problems Caused by Production Equipment and Examples of Improvements