The world's highest level of 20G vibration performance! Yacmo's control technology is used for environmental vibration countermeasures.
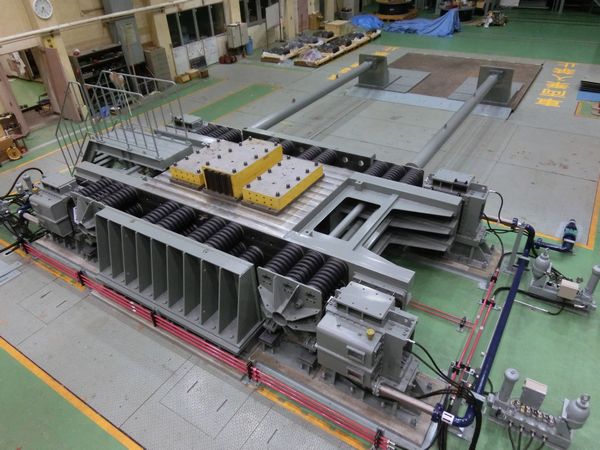
We have cooperated with the Central Research Institute of Electric Power Industry in the development of advanced control of the SAMD vibration control system for environmental vibration countermeasures for their resonance vibration table.
Yacmo's outstanding vibration control technology enables us to design and propose the optimal control system for any situation.
issue
The Central Research Institute of Electric Power Industry has developed a resonance vibration table that amplifies the acceleration of vibration by utilizing the foundation reaction force of a double-spring separate mounting system to check the seismic safety of critical nuclear equipment such as valves, and has achieved the world's highest level of vibration performance at 20G (maximum loading weight is 10 tons, The table size is 2.0m x 1.8m).
However, the facility's 10-ton mass vibrates at a very high acceleration, and there were concerns about the vibration impact on the surrounding area. Therefore, two SAMDs (semi-active mass dampers) were installed at the base of the vibration table to generate vibration in the opposite phase to that of the table, thereby suppressing the propagation of vibration to the surrounding area.
When the SAMD was first introduced, it was controlled by splitting the sine wave signal input to the resonance shaking table and manually adjusting the appropriate phase shift and gain through digital processing, but this may have required fine adjustments each time the specimen was changed, and there were concerns that the SAMD's capabilities might not be fully demonstrated. However, this may require fine-tuning each time the specimen is changed, and there was concern that the capabilities of SAMD would not be fully demonstrated.
So there,
- Ability to automatically adjust control parameters even if the specimen is changed.
- More vibration suppression performance
Yacmo has received a request for control sophistication(1)。
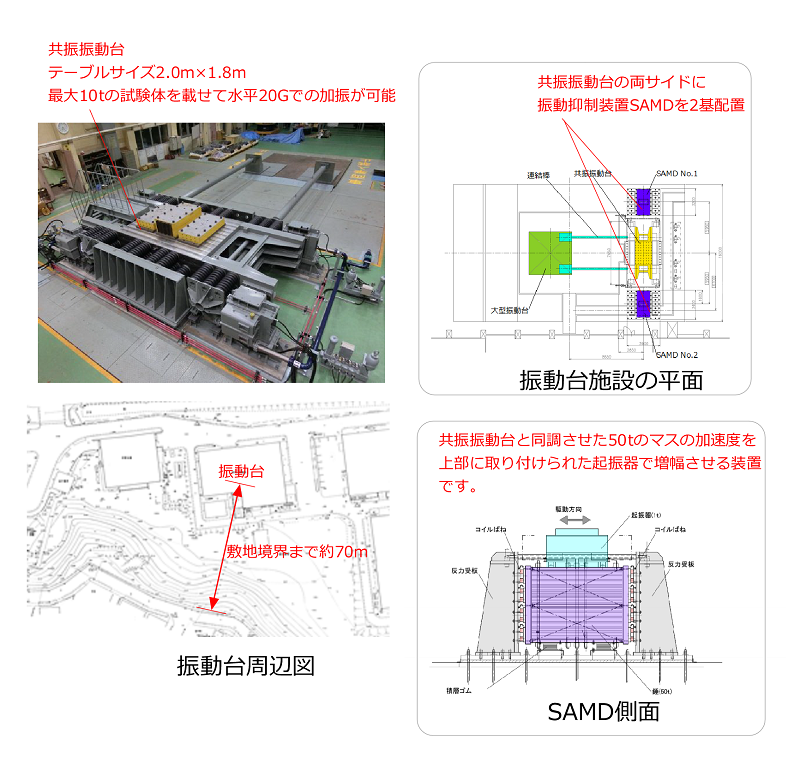
counter-measure
We started by conducting actual vibration tests and measuring the data needed for analysis. Next, we modeled the shaking table facility, repeated simulations, and analyzed how best to control SAMD.
Based on the analysis results and actual operating conditions (e.g., sinusoidal excitation, assumed nonlinearities in the control object, etc.), we decided to adopt automatic control using an adaptive digital filter and designed the control system for the case. After the design, simulations confirmed that the vibration acceleration on the shaking table foundation could be sufficiently reduced.
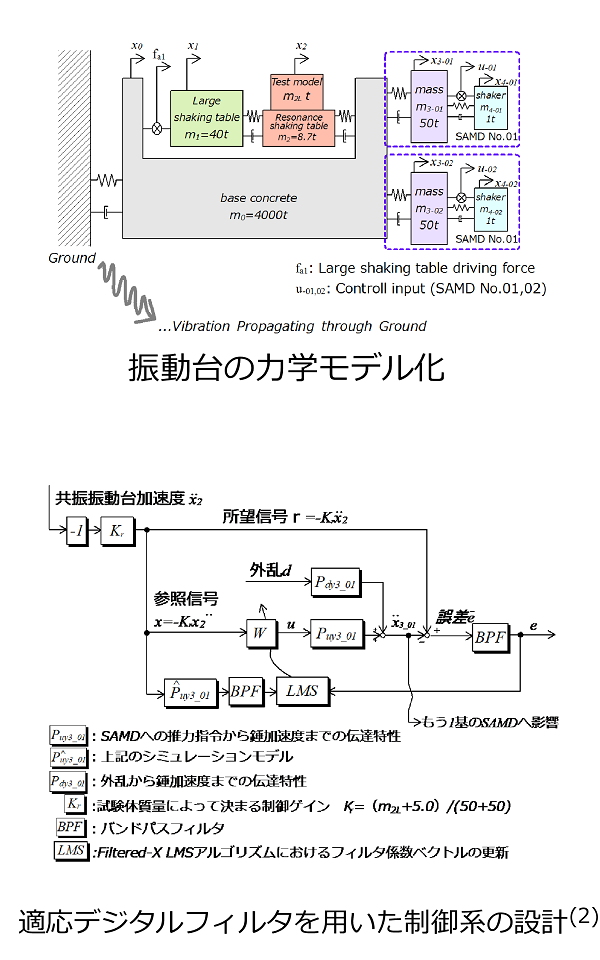
result
After mounting the control system, a 5-ton dummy mass was mounted on the resonance vibration table as a test specimen and subjected to acceleration of 10 G and 20 G. As shown below, the results were very favorable, confirming that the vibration test was possible without exceeding the vibration level regulation value (60 dB) at the site boundary.
Vibration level measurements at two points on the property line. The new control system using an adaptive digital filter has a higher vibration suppression effect than the conventional control (manual control method when SAMD was first introduced).
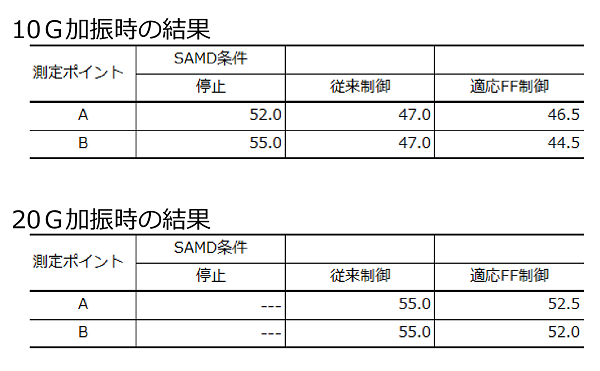
Furthermore, the spectral analysis of site boundary vibration acceleration at 10G excitation shows that a very large effect is obtained at the excitation frequency of 9.6875Hz.
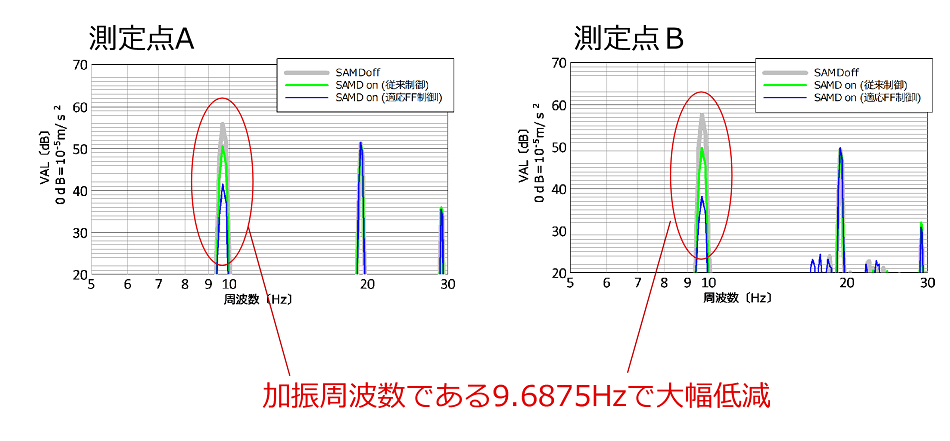
(1) Joint research with CRIEPI and Yacmo Co., Ltd. on 「Examination of upgrading semi-active mass damper control system in resonant vibration table」.
(2) Nishiyama, et al, 「Vibration Countermeasures for Resonant Vibration Table by SAMD Using Adaptive Digital Filter」, Proc. of JSME [No. 16-15] Dynamics and Design Conference 2016 USB, pp. 227-1-11, 2016-08-23